Olmsted Locks and Dam
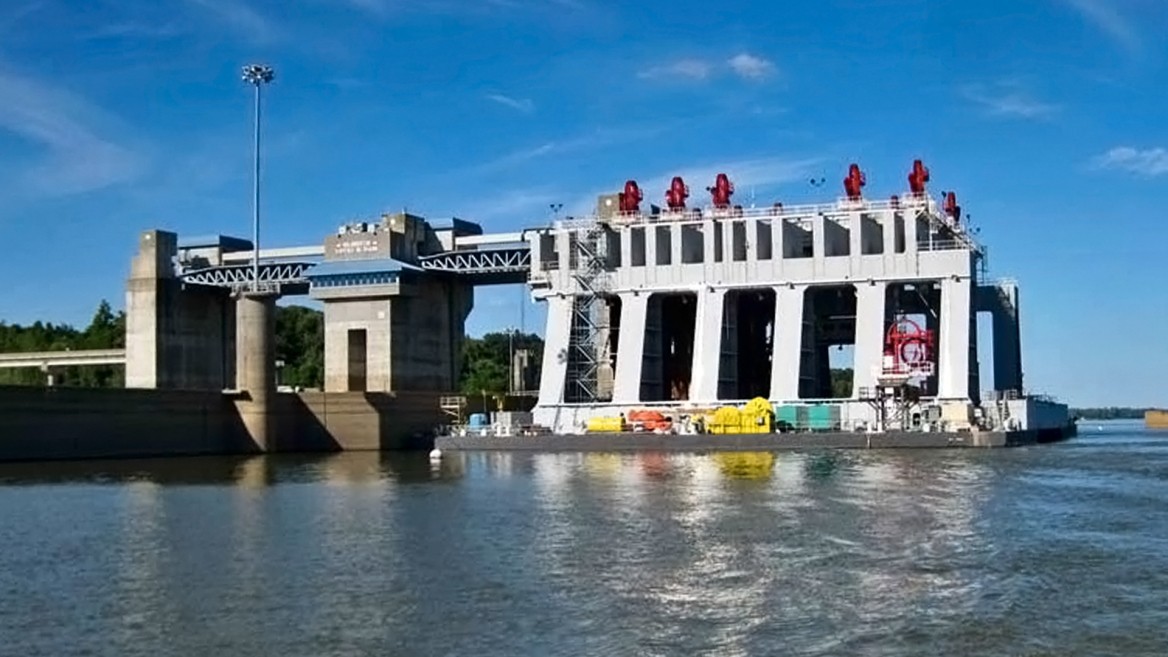
TYLin provided structural and mechanical construction engineering design, as well as detailing services for the precast concrete operations and in-the-wet construction operations, for the Olmsted Locks and Dam project.
Designed to significantly reduce tow and barge delays, the project was located between Illinois and Kentucky about 17 miles upstream of the confluence of the Ohio and Mississippi rivers. This strategic reach of the Ohio River provides a connection between the Mississippi River, Tennessee River, and Cumberland River. More tonnage passes this point than any other place in America’s inland navigation system.
The Olmsted Locks and Dam project replaced existing Ohio River Locks and Dams 52 and 53 with twin 110-foot by 1200-foot locks adjacent to the Illinois bank and a new dam. The dam comprises five tainter gates, 1400 feet of boat-operated wickets, and a fixed weir extending into the Kentucky bank.
TYLin also provided structural and mechanical engineering services for the flat jack shell support systems. The vertical positioning system, which operated alongside of and integrated with the horizontal positioning system consisted of a series of up to 24 450-ton flat jacks that allowed final positioning of the shell segments in their proper location.
To monitor uplift forces and stresses in the concrete shell during tremie concrete operations, the lifting frame and flat jacks were used as load cells. Once a shell was in position, the lifting frame was also used to complete the tremie concrete placement through the top of the shell from above-water.
Once the tremie concrete was placed beneath the shells and cured, the jacking system was transfused with epoxy, making it a permanent part of the overall monolith placement. The next segment was then moved into position.
PROJECT HIGHLIGHTS:
- TYLin’s work was under a task order type three-year contract authorized by the Water Resources Development Act of 1988 for the U.S. Army Corps of Engineers, Louisville District.
- Scope of work included a review and check of shop drawings and the development of a 3D model of the shell segment showing all rebar, embedded metals, pintles, baffle blocks, beams, tremie openings, drill collar anchorages, and air bleed holes.
- The flat jack shell support systems allowed the 116-foot by 125-foot precast shell segments to be positioned and aligned under several feet of fast-moving water.
- A complete set of redundant jacks, hydraulics, and controls were included for the vertical positioning system in the event of master system failure.
- The flat jacks were controlled from the above-water catamaran barge that transported the shells to their permanent location in the river.
Services
- Construction inspection
- Civil engineering
- Structural engineering
- Construction engineering
- Gantries, cranes and special lifting fixtures
- Construction management
- Studies